Aircraft engines enjoy a luxury of precaution in their handling and transport. These are high-value items that have both large parts to protect and smaller, more fragile, high-tech mechanisms that are very exposed during transport. Shrinking is the most popular method to date, as it provides all the guarantees that the parts arrive at their destination in perfect condition.
What is aircraft engine shrink wrapping?
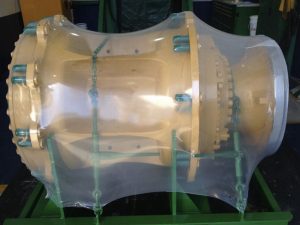
Turbine shrink-wrapped in transparent film
Shrink wrapping means to wrap an object with shrink film, which is then heated with a specific gun. When heated, the film shrinks and takes the shape of the object to be protected, then hardens. It forms a watertight layer, like a shell, which ensures that no contaminants can enter.
The use of shrink film helps to protect sensitive components from the causes of damage during transport or storage, such as contamination by dust and dirt, weather, humidity, heat, extreme cold, UV rays, knocks and bumps, etc.
For high-value industrial parts such as aircraft engines, the films also contain reinforced UV inhibitors, so the parts can withstand exposure to the sun and the very high temperatures of some countries.
The advantages of shrink film for the aeronautics industry
The shrink wrapping of aircraft engines – and aircraft components in general – makes it possible to transport them by any means, including truck, plane or boat. It is possible to shrink wrap an item in one piece or to transport parts separately. These are then no longer protected within their housing and are sensitive to weather conditions that they would not normally be exposed to during the flight. This is the case when there is maintenance to be carried out on spare parts, or to bring together parts from various sources for their final assembly.
During sea transport, shrink wrapping fully protects parts against humidity and sea air, which are particularly corrosive. Shrink films for aviation applications are extremely strong and flame retardant. Their thickness is about 250 microns and above.
Aeronautical parts to be shrink wrapped
Internal parts
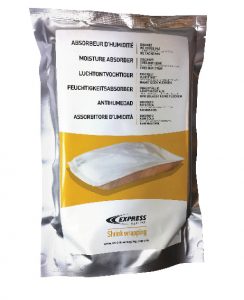
Moisture absorber
When the aircraft engine is dismantled prior to transport, shrink wrapping protects parts that are normally internal, such as computer components, electronics and ferrous metals. It is therefore necessary to determine which elements require specific forms of protection.
In the case of parts that are particularly sensitive to humidity, for example, it is possible to add desiccant bags that will absorb the moisture. Some metal parts that are sensitive to corrosion must also be protected using VCIs (volatile corrosion inhibitors).
External parties
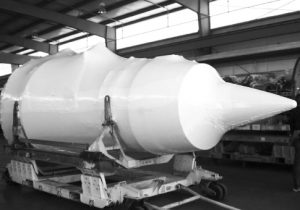
Turbine shrink-wrapped in transparent film
For the external parts of the engine, shrink wrap is usually not applied directly to its casing; padding is provided between the shrink film and the engine to give it better protection.
The padding protects the engine from direct contact with the plastic, which can rub the painted parts. It shields it from knocks and bumps during transport, which can cause denting or tear the plastic and damage the casing.
The padding also creates a thermal barrier against extreme temperatures. Elsewhere, transparent film may be used to enable inspection of the contents.
Professional installation techniques
To shrink wrap large aeronautical parts, large professional machines must be used. Companies working in this field provide comprehensive services, including the supply and application of specific polypropylene films.